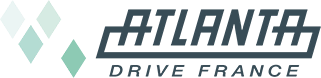
Dossier de presse
Janvier 2023
Scellage thermoplastique à impulsion ROPEX® : 2 technologies de pointe à la conquête du marché français
De nouvelles solutions de thermoscellage par impulsion ROPEX® sont lancées sur le marché français par Atlanta Drive France, une exclusivité qui offre de nouvelles opportunités dans le process du scellage de poches en plastique et notamment dans les applications complexes de scellage à chaud. Les technologies à impulsion RESISTRON® et CIRUS® du fabricant allemand ROPEX® profitent de développements standards et sur mesure qui s’intègrent aux machines pour l’industrie agroalimentaire, médicale, pharmaceutique, cosmétique, automobile et nouvelle mobilité, …


Adaptabilité maximum
Les emballages modernes doivent répondre à des exigences de plus en plus élevées : machines à haut rendement, applications d’emballage spéciales, exigences particulières des produits emballés, pression croissante des couts de production, types de films de plus en plus fins et donc sensibles, temps de scellage les plus courts possibles, stress thermique minimal pour les produits emballés, réduction des temps d’arrêt pour maintenance, remplacement des pièces d’usure ou ré-outillage, … Le système de scellage et le processus de répétabilité doivent répondre à des défis de taille pour être garantis.
ROPEX® a acquis sa notoriété mondiale comme développeur de régulateurs de température sans capteur pour le scellage des thermoplastiques par la méthode des impulsions – RESISTRON® puis CIRUS®. Une innovation qui a également inspiré de nombreux autres types de régulateurs de température offrant de nombreuses fonctionnalités et une connectivité étendue.
Le procédé de scellage par impulsion est une alternative très intéressante aux outils de scellage classiques (chauffe en continu) ; il offre de nombreux avantages, notamment dans les applications complexes de scellage à chaud.
3 composants stratégiques
La barre de thermoscellage :
elle doit s'intégrer précisément dans l'environnement de la machine. Le développement des barres de soudure se fait en collaboration avec les clients. Les essais de soudure sont effectués dans notre laboratoire d'essai en utilisant le film réel.
L'outil de scellage RSE :
c’est une barre de scellage avec une bande de scellage et une contre-barre correspondante qui se combinent avec les composants du système existants pour recréer un environnement sur mesure performant.
Le régulateur de température RSE :
il permet de générer des impulsions électriques de quelques centaines de millisecondes avec une dynamique de température allant jusqu’à 6000 K/s et offre ainsi un contrôle très précis de la température lors du thermoscellage. Le régulateur convient également pour le scellage en continu de systèmes à air chaud.
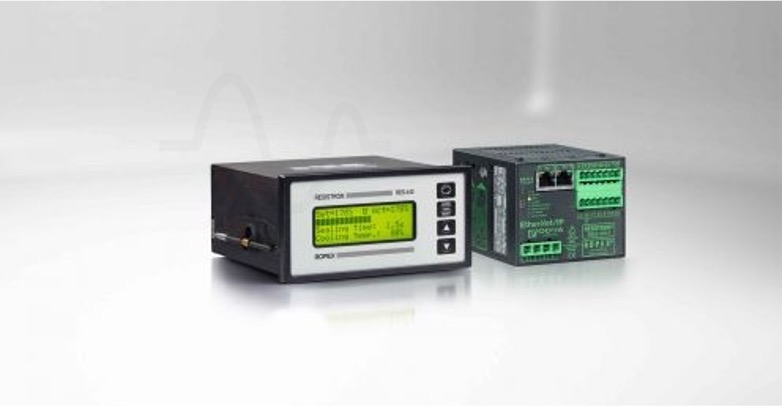
2 technologies complémentaires pour toutes les applications
Technologie resistron®
- Longueur de scellage jusqu’à 7 m
- Largeur de scellage jusqu’à 40 mm
- Profil de scellage 1D, 2D & 3D (possibilité d’insertion de becs, tubes, …)
- Cadence maxi. 80 cycles par minute
- Scellage d’épaisseurs non uniformes
- Refroidissement de la soudure possible
- Combinaison coupe et scellage
- Soudage sur les deux faces pour les applications films épais, avec insert entre deux films, …
Technologie cirus®
- Longueur de scellage jusqu’à 1m
- Largeur de scellage 6 mm maxi.
- Profil de scellage 1D & 2D
- Cadence maxi.120 cycles par minute
- Scellage d’épaisseurs non uniformes
- Refroidissement ultra-rapide de la soudure par source réfrigérée externe (eau)
- Combinaison coupe et scellage
- Pas de pièce mobile
- Nettoyage facile
- Résistance à l’humidité
Chauffage continu ou scellage par impulsion ?
Le thermoscellage par impulsion est une technologie plus précise et efficiente que le scellage thermique en continu ou le scellage par ultra son. Il offre des fonctionnalités que ne propose pas le scellage continu, à savoir :
- Des soudure complexes comme les soudures perpendiculaires, circulaires, ou complexes dans les angles ou le scellage de matériaux traditionnellement compliqués à sceller, comme les nouveaux plastiques bio recyclés.
- Un contrôle de la température et une mise en service instantanée
- Une sécurité renforcée de la température des barres de scellage : la barre n’est pas en permanence à 300°C
- Une cadence supérieure
- Un coût d’investissement medium par rapport au scellage par ultrason plus cher et le scellage thermique continu moins couteux
- La fonction de « coupe » peut être associée au scellage.
- Un process moins énergivore et plus économique
Chauffage continue
versus
scellage par impulsion
Non contrôlé

Précision de la température
Contrôle précis
Boucle ouverte

Contrôle de la température
Boucle fermée
Procédés séparés

Coupe & scellage
Intégrés dans le même process
Format fixe

Variation de taille de poches
Format indépendant
Scellages déviants

Reproductibilité
Scellages identiques
Risques de coupures et brulures

Sécurité des postes de travail
Pas de risque de coupures ou brulures
Une zone continue

Zones de chauffe
Plusieurs zones définies
Usage excessif de film

Usage de film
Pas d’excès de matériaux
Des bandes de scellage étroites et résistantes pour économiser le film
Les concepteurs de produits, les fabricants de films et les entreprises technologiques telles que ROPEX® travaillent en R&D pour fournir des solutions innovantes répondant à la problématique de durabilité des emballages.
Cela inclut des efforts pour réduire la largeur de la zone de film à sceller afin d’économiser du matériau d’emballage dans la zone de scellage supérieure, latérale et inférieure. Pour les soudures étroites, la technologie de scellage utilisée doit répondre aux exigences les plus élevées en matière de scellage, telles que la résistance à la traction et l’étanchéité au gaz, tout en offrant une qualité visuelle attrayante.
Les outils de scellage par impulsion de ROPEX® offrent comme performances une résolution élevée de la température dans la zone active, un impact thermique minimal – tant sur le film que sur le produit – et une qualité de scellage élevée même avec les plus petits contours de scellage.
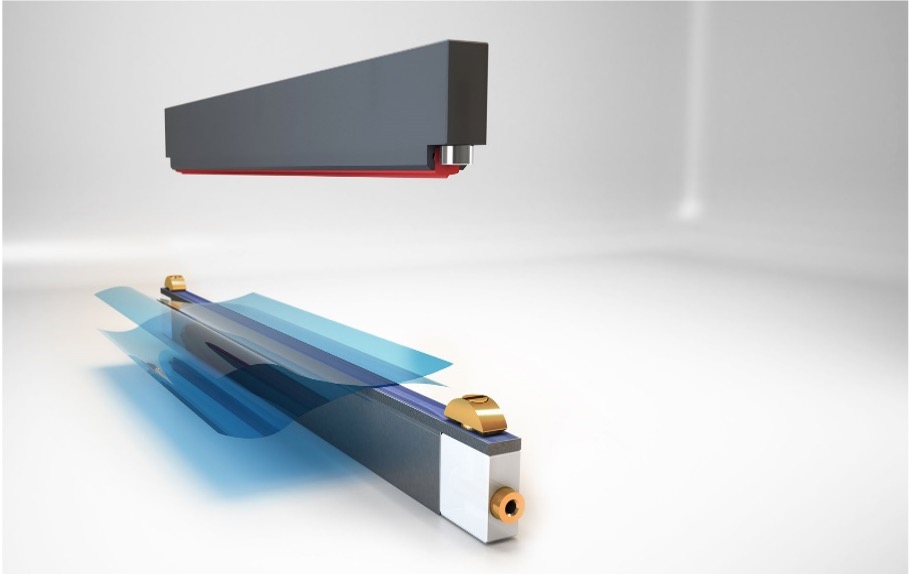
Scellage de matériaux monocouches, l’enjeu pour un recyclage optimisé
La récupération des matières plastiques par le recyclage est aujourd’hui un objectif majeur. La clé d’un recyclage réussi réside dans la séparation et le fractionnement des déchets en leurs matières premières d’origine, qui sont ensuite prêtes pour un traitement ultérieur direct dans la chaîne de recyclage. Les composites complexes posent un défi particulier car ils doivent être séparés en leurs composants avec des coûts conséquents.
Les matériaux d’emballage multicouches couramment utilisés dans l’industrie de l’emballage constituent l’un de ces défis. De nombreux films multicouches offrent différentes propriétés de barrière, par exemple les emballages alimentaires en PE/PA, qui prolongent considérablement la durée de conservation des aliments emballés. L’ajout de PA à la solution multicouche réduit également de manière significative l’épaisseur totale de la couche et améliore ainsi la stabilité mécanique du film. L’utilisation de couches d’aluminium dans la solution multicouche rend également le processus de recyclage ultérieur beaucoup plus difficile.
Les fabricants de films travaillent au développement de films mono-matériaux qui atteignent des propriétés barrières suffisantes avec de faibles épaisseurs de couche. Ces propriétés barrières requises pour le produit emballé peuvent également être obtenues, par exemple, par un revêtement de films biodégradables avec des revêtements fonctionnels à haute performance.
À cette fin, ROPEX® travaille avec des partenaires sur des solutions qui combinent de manière optimale les avantages des matériaux monocouches enduits avec la capacité de scellage par impulsion – vers une solution globale pour les entreprises d’emballage.
Les emballages de demain en plastique recyclé ?
Avec les nouvelles normes européennes et internationales sur le
recyclage des déchets plastiques et la production de plastique recyclés, la production de films plastiques va évoluer vers plus de matériaux recyclés. La Directive européenne Packaging and Packaging Waste Directive préconise par exemple de recycler 55 % des emballages plastiques d’ici à 2030.
Cette tendance va également influencer la composition des films plastiques utilisés dans l’industrie de l’emballage, et de ce fait avoir une incidence sur les caractéristiques de scellage de films. Pour sceller les films thermoplastiques, une certaine température est nécessaire pour définir la fenêtre de traitement du matériau.
La technologie de scellage par impulsion ROPEX®, répond à ces nouvelles contraintes avec un contrôle précis
de la température et du temps
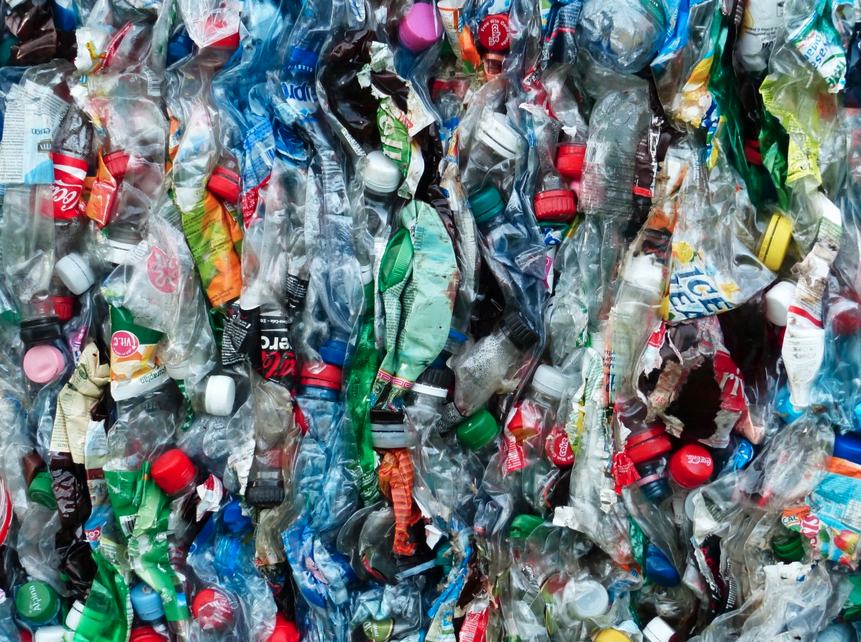
Les bio-films biodégradables adaptés au scellage industriel
Pour l’industrie de transformation, les grands atouts des plastiques tels que la stabilité, la persistance et l’inertie sont précisément les facteurs qui entravent la décomposition ou la dégradation des polymères.
Les biofilms en plastique biodégradable possèdent les mêmes caractéristiques physiques que les films plastiques traditionnels : robustesse et durabilité. Ils apportent en plus une alternative pertinente sur le plan de la décomposition et de l’empreinte écologique, car ils sont compostables tout en étant résistant à la chaleur. La dégradation biologique de ces polymères se fait par hydrolyse des chaînes de polymères en de nombreux fragments plus petits, qui sont pour la plupart solubles dans l’eau. Ils peuvent ensuite être absorbés par les cellules et se dégrader davantage.
L’introduction ou la conversion en films biodégradables de ce type nécessite une entrée de température précise, une fenêtre de processus contrôlable et une force de scellage complètement intégrée par la technologie de scellage par impulsion ROPEX®.
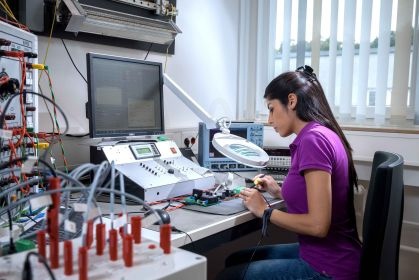
Empreinte CO2 : une production optimisée sur le plan énergétique
Chaque produit emballé dans un film plastique a été scellé par la fusion d’un thermoplastique. Il faut de l’énergie sous la forme d’un apport de température au matériau pour faire fondre les deux couches de film ensemble.
La majorité des systèmes sur le marché utilisent un procédé de scellage très simple qui fournit une certaine température en continu, indépendamment de la demande. Cependant, le processus d’emballage est un processus intermittent qui ne nécessite que l’énergie nécessaire pour sceller dans la milliseconde en cas de contact.
Des solutions intelligentes sont nécessaires pour garantir le succès des efforts des entreprises d’emballage pour parvenir à une production efficace et écologique. La technologie de scellage par impulsion de ROPEX® garantit que la chaleur n’est générée qu’au moment du contact du film avec l’outil de scellage et de la demande réelle de chaleur. En dehors du temps de l’impulsion, le système de scellage reste froid : une production de chaleur à la demande optimisée sur le plan énergétique et empreinte CO2.
« le lancement d’un plan de sobriété énergétique pour réduire de 10% notre consommation, première marche avant une réduction de 40% d’ici 2050 ». https://www.ecologie.gouv.fr/sobriete-energetique-groupe-travail-industrie
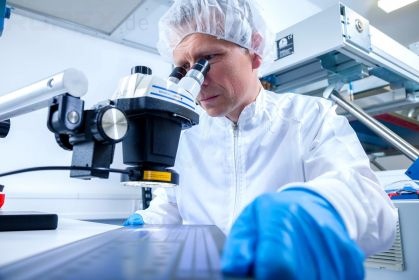
Nouveaux matériaux pour Solutions d'emballage
Les bioplastiques,
peuvent être produits à partir d’une variété de plantes naturelles et de matières premières biologiques. Les principaux fournisseurs de matières premières sont le bois (cellulose et lignine), les plantes céréalières et les pommes de terre (amidon), la canne à sucre et la betterave sucrière (sucre) et les plantes oléagineuses (huiles végétales).
Les biopolymères,
à base de bois apportent une approche prometteuse : la ressource naturelle renouvelable la plus abondante au monde est la cellulose, qui peut être extraite du bois. Il y a environ 150 ans, les premiers bioplastiques modernes ont été développés à partir de la cellulose. Le plus connu est probablement la « cellophane » (cellulose régénérée), qui est passée d’un simple film de bonbon à un film d’emballage moderne et multifonctionnel.
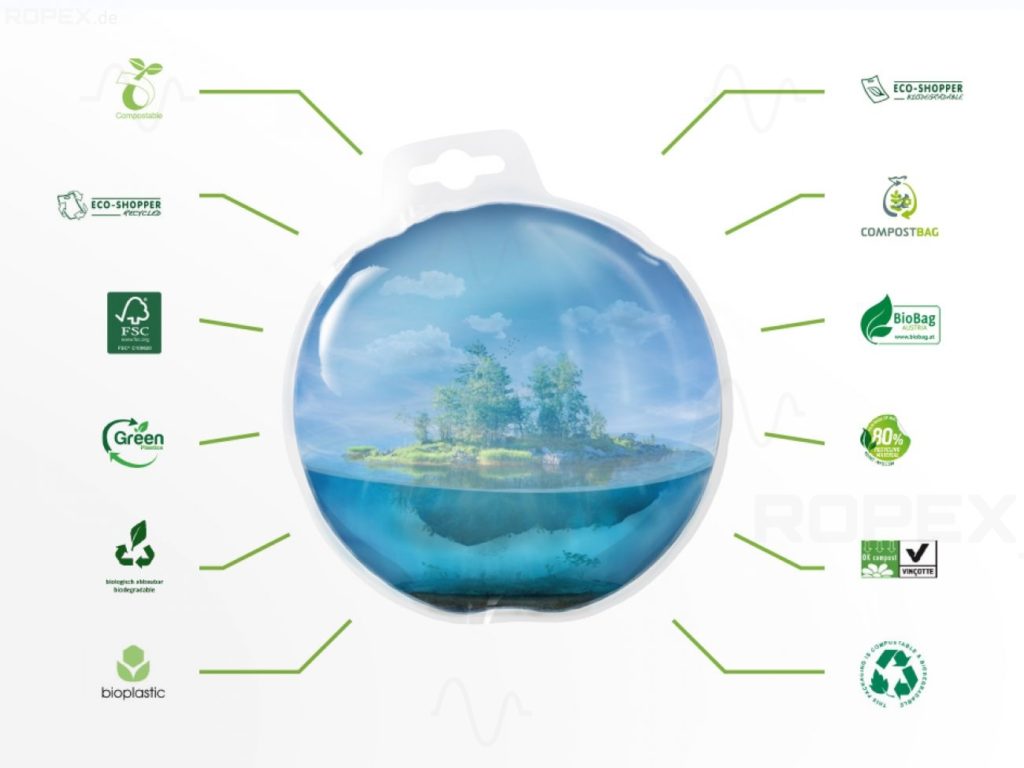
Dans le secteur de l’emballage des aliments secs, des technologies pour des matériaux en papier à haute performance sont déjà disponibles aujourd’hui. Ici aussi, l’accent est mis sur la fermeture des sacs d’emballage afin que le produit arrive au consommateur en toute sécurité.
Dans le choix d’emballages en papier respectueux de l’environnement, l’engagement en faveur d’offres durables sans plastique joue un rôle particulièrement important. Les emballages en papier sont de plus en plus populaires, notamment dans les magasins d’aliments naturels, les supermarchés bio et les épiceries fines. Les solutions de scellage ROPEX® permettent de transformer un agent d’étanchéité entre les couches de papier en un emballage hermétique. Habituellement, un mince revêtement de PE, une couche de cire, une application de résine, une solution à base de sucre ou même un hot-melt sont stimulés pour réagir, généralement par une impulsion thermique contrôlée.
Compagny profils
Atlanta drive france
ADF filiale française de la société allemande Atlanta GmbH, fabricant spécialiste des crémaillères de précision, et des réducteurs à vis sans fin à jeu réduit, disposant d’une offre très large le domaine des techniques de transmission. ADF est membre du syndicat des industriels de la mécatronique, ARTEMA.
- 12 000 références
- CA 2019 France : 2,5 M€
- Date de création : 2005
ROPEX®
ROPEX® Industrie-Elektronik GmbH est sur le marché international du scellage des thermoplastiques depuis sa création en 1976, en Allemagne. La société de renommée internationale développe des solutions de scellage des thermoplastiques par la méthode d’impulsion avec des régulateurs de température sans capteur.
- CA 2020 : 8,1 M$
- Date de création : 1976
chiffres clés ADF
contact RELATIONS presse
Laurence THOLLET
Attachée de presse
laurence@2lagence.com
+33 (0)6 22 71 52 81 // +33 (0)4 79 72 60 70
- ATLANTA Drive France
-
9 rue Georges Charpak
77127 Lieusaint - 01 64 05 36 16
- info@atlanta-drive.fr